from slipping out of place when the platen first presses
against the edge of the paper, and start the printing cycle
as described previously. After the printing cycle is
completed, remove the paper for processing. Any
number of duplicate prints can be made by repeating the
printing cycle.
Drop the print, emulsion-side down, into the
developer. Immerse it immediately with a quick sliding
motion while pushing the print under the surface of the
solution. Grasp one edge of the print, lift it up, and turn
it over. Replace the print emulsion up on the surface of
the solution. Push the print under the surface again and
leave it under during the remaining time in the
developing tray. The print must be immersed rapidly and
evenly to prevent air bubbles from forming on the
emulsion surface. Be sure that all the emulsion gets wet
with the developer in the shortest time. Agitate the print
constantly for the remaining developing time.
Each type of printing paper has its own working
characteristic. The main difference in each type is the
length of time required for the image to develop in a
given type and strength of developer. A correct print is
one that develops to the proper density and contrast in
the recommended time. A print should be exposed so it
reaches the proper density and contrast only with full
development; otherwise, the tone and appearance of the
print will be below acceptable standards. If the exposure
is insufficient, the image does not develop to the desired
density even with longer developing time. It appears
pale and lacking in brilliance. Also, stains may occur
when development is carried out too long. Paper
developers work more rapidly than those used for films;
consequently, print immersion must be quick and even,
and agitation should be constant.
When the print is fully developed, lift it out of the
developer, drain it momentarily, and place it in the stop
bath. After about 5 seconds in the stop bath, lift the print,
drain it briefly, and place it in the fixing bath. Agitate it
in the fixing bath for a few seconds and examine it for
defects that might cause it to be discarded. When the
inspection is completed, place it emulsion-side down in
the fixer and complete the fixing process. Follow the
manufacturers instructions as to the required fixing
time. Fixing for Ilford Multigrade paper is complete
after about 30 seconds in fresh fixer.
Some papers have a tendency to float in the fixing
bath, especially if the bath is mixed a little stronger than
usual. When prints float in the fixer, they should be
handled constantly or turned facedown to prevent the
emulsion from being exposed to the air. The parts of a
print exposed to the air during fixing may become
stained
Prints that float facedown should not create
problems except for the chance that air bubbles can be
trapped under the prints. Air bubbles under a print
produce stains and must be prevented. By immersing the
prints edgewise and facedown, you eliminate air
bubbles.
CAUTION
Never attempt to work backwards through
the sink-line process. A few drops of fixer on
your hands or from a print will contaminate the
developer.
Group Print Development
Several prints can be processed at one time,
provided they are separated and agitated sufficiently
during the process. Each entire print must be wetted
uniformly by the solutions so all parts of each print are
processed uniformly.
When you are processing several prints at one time,
immerse them in the developer separately at regular
intervals and, at the end of the proper developing time,
remove the prints in the same order and at the same
regular intervals. To prevent the prints from sticking
together, you should let each one be completely
immersed before the next print is put in the developer.
Agitation should be done by rotating the prints in the
solution. To do this, take each print, in turn, from the
bottom of the tray and place it on top of the other prints.
As the prints reach full development, transfer them
one by one to the stop bath. Treat them for 10 to 20
seconds; then place them in the fixer and agitate each
print to make sure none of them stick together.
After the prints are fixed, they must be washed and
dried. The RC or polyethylene coating on paper prevents
absorption; therefore, they require a short wash time.
Wash prints for 2 minutes in a good supply of running
water to ensure they are completely free of chemicals.
The water temperature should not be lower than 41°F
(5°C). Prints may be dried in a print dryer designed for
polyethylene or RC papers not to exceed 190°F (68°C).
Adjust the print dryer to the minimum temperature
required to dry the paper sufficiently. If the print dryer
is too hot, the polyethylene coating on the paper will
melt. When a paper dryer is not available, remove the
excess water and dry the prints naturally at room
11-7
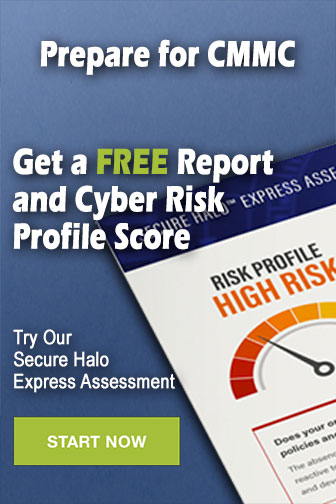