Unlike black-and-white film processing, color
negative film cannot be push processed successfully;
therefore, you must choose a film with an appropriate
film speed for the lighting conditions in which you
photograph your subject.
COLOR REVERSAL FILM PROCESSING
Color transparency film forms dyes according to a
reversed silver positive; for example, a yellow dye
image forms in the top emulsion that corresponds to an
absence of blue in the original scene. This yellow dye
subtracts blue light. A blue image is formed by magenta
dye (minus green) and cyan dye (minus red), thus
leaving blue. In color transparency film, the dyes
subtractively produce a correct color positive image of
the scene photographed.
The Kodak E-6 Process is used in the Navy for
processing color reversal film. There are seven chemical
steps and two wash cycles in the Kodak E-6 Process.
They are as follows:
first developer, wash, reversal
bath, color developer, prebleach, bleach, fixer, wash,
and final rinse.
The first chemical step is the first developer. The
first developer is a black-and-white developer that
converts the exposed latent image in each emulsion
layer to a metallic silver. Like black-and-white negative
processing, after the film leaves the first developer, there
are undeveloped areas where the silver halides are
unaffected by camera exposure. It is these undeveloped
areas that the final color positive images are formed in
reversal film.
After the first developer, the film is chemically
fogged or re-exposed in the reversal bath. The reversal
bath exposes the silver halides that were not developed
in the first developer. This re-exposure is what forms the
positive image. After 1 minute in the reversal bath, the
normal room lights can be turned on.
After fogging, the film is developed in a color
developer. The color developer works the same way in
color reversal processing as it does in color negative
processing. It changes the fogged silver halides to black
metallic silver and at the same time, cyan, magenta, and
yellow dye couplers are formed by the exhausted
developer.
At this stage the film looks completely black
because the formed dyes are shielded by the developed
silver. The film is then placed in a prebleach. The
prebleach prepares the film for the bleach and also
stabilizes the dye layers.
The metallic silver is removed by the bleach and
fixer processes. The bleach and fixer work the same way
as they do for color negative processing. After the silver
is removed, only the dyes remain, forming the image.
The film is then washed to rinse away any remaining
chemistry and soluble silver. The last chemical step in
the E-6 process is the final rinse. Final rinse provides a
wetting agent to aid in uniform drying.
It is possible to push process (underexpose and
overdevelop) or pull process (overexpose and
underdevelop) most color reversal film; however, some
sacrifice in quality results in "push processing." Less
detail in the shadow areas (weaker blacks), less
exposure latitude, and noticeably increased grain occur
when color reversal film is "push processed." When the
film speed is altered, only the first developer time is
changed. All other chemical steps remain the same. You
should not exceed two f/stops when you intend on
push or pull processing.
MACHINE PROCESSING
Today most film processing is performed by
machine, especially in larger imaging facilities.
Machine processing has many advantages compared to
hand processing. Machines can process high-volume
production more efficiently and more consistently
compared to hand processing. When machines are used,
the variables involved in processing can be controlled
more easily. Time, temperature, and agitation can be
kept constant if the machine is properly maintained and
operated properly. With fully automatic processing
machines, all you must do is feed the film or paper into
the machine and retrieve the finished product.
When there are advantages, there are also
disadvantages to machine processing. Machines require
maintenance, can jam, occupy precious shipboard
space, and may require special plumbing, ventilation, or
power requirements. The need for proper maintenance
is most critical. Poor equipment maintenance is
probably the major cause of machine processing
problems. Therefore, it is very important for scheduled
preventive maintenance to be performed properly on all
imaging equipment, especially automatic processors.
The best images captured by a camera are not of any use
if they are not processed correctly and without defects.
You must be qualified completely in the Planned
Maintenance System (PMS) to become a valuable
member of an imaging facility.
In a high-volume production facility, the advantages
of automation far outweigh the disadvantages. There are
10-27
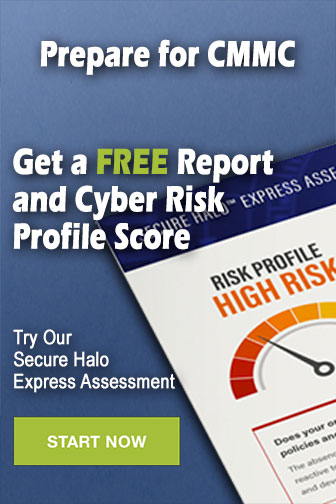