The chemistry most commonly used in the Navy for
color paper processing is Kodak Ektacolor RA
Chemicals for Process RA-4. The RA-4 process is a
washless process that consists of color developer,
bleach/fix, and stabilizer. The total processing time for
the RA-4 process is about 4 1/2 minutes.
Transparencies that are old or stored under adverse
conditions are likely to fade to some degree. This fading
may not have been equal overall. That can create
problems in printing. Generally, slide duplicates vary
widely in quality and do not make high-quality color
prints.
MAKING TRANSPARENCIES FROM
COLOR NEGATIVES
You can make brilliant color transparencies from
color negatives as easily as you made color reflection
prints by using color printing materials on a transparent
film base. These transparencies are of excellent quality.
This allows you the option of making them larger,
smaller, or the same size as the original negative.
There are several direct positive materials available
for making color prints directly from color slides. Kodak
Ektachrome 22 paper is a reversal color paper that, when
exposed to a slide, produces a positive color image of
the slide. Kodak Ektachrome 22 paper is processed in
Kodak Ektachrome R-3000 chemicals. Consult the
Photo-Lab-Index for the most updated information
concerning these processes.
Several materials are available for making color
transparencies from color negatives. Two of the most
common are Kodak Duratran RA and Kodak Duraclear
RA display materials. These materials allow you to
make large-display transparencies from color negatives.
Another way to make full-color prints directly from
color transparencies is by the dye destruction color
process. At the time this training manual was written,
Cibachrome products are the only direct positive color
materials manufactured using this process.
The Kodak Duratran RA and the Duraclear RA
transparency materials can be printed using the same
methods, printing equipment, and processing chemicals
as Duraflex RA print paper. Both the transparencies and
paper are processed using Kodak Ektacolor RA-4
chemicals; however, the transparency materials require
a longer processing time. The Kreonite Model KCP-16
allows for this longer processing time. By flipping a
switch, you can slow down the processor, allowing for
a longer processing time.
12-14
Cibachrome silver-dye-bleach materials consist of
a white opaque support, coated with light-sensitive
emulsion layers on one side and a matte, anticurl gelatin
on the opposite side. This white pigmented plastic film
base has a similar appearance to paper but is actually a
film, much like color slide materials-the emulsion
layers are arranged in the same order as color
transparency (slide) materials (including the yellow
filter layer).
When printing color transparency materials, you
must use a black easel. Because these materials do not
have a paper backing, light is transmitted through the
material and reflects back when a black easel is not used.
All other printing steps are the same in printing color
paper and color transparency materials. Consult the
Photo-Lab-Index for starting exposure and filter pack
settings.
Unlike conventional color paper processes where
dyes are formed from color couplers during processing,
dyes in Cibachrome materials are incorporated in the
blue, green, and red light-sensitive layers during
manufacturing. These cyan, magenta, and yellow dyes
are designed to be destroyed when processed. Red
exposure is intended to cause the destruction of cyan
dyes, green exposure leads to the destruction of magenta
dyes, and blue exposure sets up the destruction of yellow
dyes.
COLOR PRINTS FROM COLOR
TRANSPARENCIES
Color prints can be made directly from color
transparencies (slides) without the time and expense of
making an internegative, but the quality of a print can
only be as good as the quality of the transparency from
which the print is made. Originals that are poorly
exposed or processed or are damaged or dusty do not
provide satisfactory prints.
The processing of Cibachrome materials involves
four chemical steps:
black-and-white developer,
bleach, fixer, and stabilizer. In the black-and-white
developer, the exposed silver halide crystals are reduced
to metallic silver. When the silver halides in the
emulsion layers are converted to metallic silver, the dyes
present in the emulsions are fragmented. In the bleach,
the silver image is converted back to silver salts
(halides), and the dye fragments are made either
colorless or water soluble. The unwanted silver salts
(halides) are then removed in the fixer. The stabilizer
keeps the remaining color dyes more permanent.
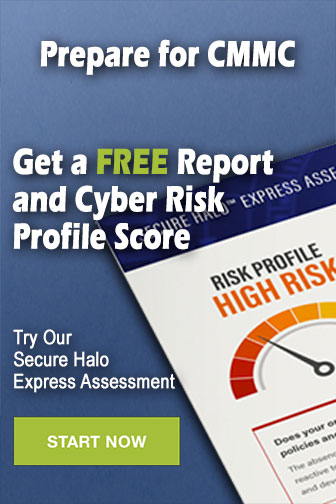