5. Subtract the initial reference values from the
averaged, processed control-strip density values.
When a control parameter of high density minus low
density is specified for the process, determine that
also. The results of these subtractions are known as
the aim values. The example in figure 2-17
summarizes steps 1 through 5 to show you how the
aim- or center-line values are derived for an LD step.
In the example below, LD red plots four lines
below the center line, LD green plots one line above
the center line, and LD blue plots one line below the
center line.
6. Adjustment tolerances may be applied to the
aim values, as appropriate, to bring the control-strip
values closer to the aim values. These adjustment
tolerances are specified in each process-monitoring
manual. For example, the red low-density (LD) value
for your processed control strip is 0.28. The adjusted
reference value is 0.32. The process-monitoring
manual indicates that the aim-value adjustment
tolerance for LD is ±.04. You can adjust the red
center-line value by subtracting 0.04 from the adjusted
reference values (0.32 0.04 = 0.28). The adjusted
aim value of 0.28 is your new center line or aim value
on your control chart.
NOTE: The adjustment tolerances change for
each step and each type of process. You must consult
the appropriate process-monitoring manual to obtain
these tolerances.
7. Tolerance limits are defined and prescribed in
each process-monitoring manual. When the average
control values obtained in the preceding step fall
within the tolerance limits, production work may be
processed and the initial reference values may be used
to determine future control values for that particular
code of control strips.
8. When average control values fall outside
tolerance limits, it is likely that there is a mistake in
the following: reading the control strips, performing
the calculations, setting up the densitometer, or
starting up the process. If errors are not detected,
there may be something wrong with the control strip.
Improper storage or handling may be the problem. If
possible, start over and use a new batch of control
strips.
Red
Green
Blue
Initial reference strip readings of LD
(averaged)
0.31
0.52
0.70
Correction factors of LD
+0.01
-0.01
Adjusted reference values
0.32
0.51
LD readings of five processed control
strips (averaged)
0.28
0.21
Adjusted reference values minus
processed control-strip values
+0.04
+0.01
0.00
0.70
0.69
-0.01
Figure 2-17.Deriving LD aim values for a process-monitoring chart.
2-33
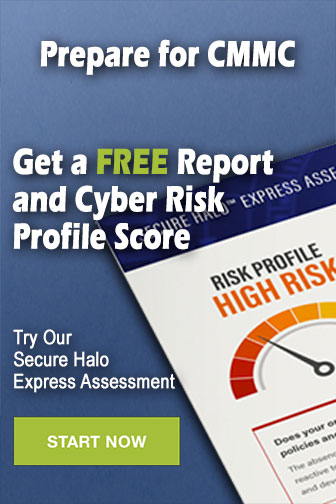