9. When the source of the out-of-control
condition is found and corrected, repeat procedures in
steps 1 through 6.
LIMITS AND TOLERANCES
Once the mean or standard has been established,
action and control limits are set according to the
appropriate monitoring manual. The action limits act
as "early warning" limits. Production work can still
be processed when the action limit is exceeded, but
this indicates that a condition exists that needs to be
corrected or the process may drift out of control.
Once the process drifts out of control, you should stop
production until the problem is corrected. If a control
strip shows that the control limits have been exceeded,
confirm this with a second strip; then refer to the
appropriate monitoring manual and stop production
until the trouble is corrected.
As you continue to plot control values, you will
see a random variation around the process mean over
which you have little control. As long as the control
limits are not exceeded, acceptable quality can be
expected.
COLOR PROCESS CONTROL CHARTS
A good control program uses control charts and
subjective print quality analysis in decision making.
A control chart provides a tool to avoid situations
where a serious processing error is compensated for in
printing to keep print quality acceptable. An imaging
facility that is compensating for errors near or beyond
the control limits is certain to have more quality
problems than a facility operating within acceptable
standards.
Preparing a control chart, such as the Kodak Color
Process Record Form, No. Y-55, is quite easy.
Follow this 8-step procedure:
1. Use a separate chart for each processing
machine.
2. Record the reference strip code number and
the reference values in the appropriate places. Use
color pencils to distinguish the red, green, and blue
densities when recording the reference values.
3. Draw horizontal lines to represent the mean,
action limits, and upper- and lower-control limits.
4. Record the process and machine number.
5. When plotting the control values, record the
date and time that the control strip was processed (not
read), and note any chemical or mechanical changes
made as a result of the plots.
6. Plot control values having a plus sign above
the line that represents the reference value, and plot
control values with a minus sign below the reference
value line.
7. Connect the points to provide a continuous
graph.
8. When changing to a new control strip code
number, note it on the chart. Record the date and the
new reference values and limits.
The control charts shown in figure 2-18 are not
intended to represent an actual control film or process.
It is used for illustration purposes only to show
patterns that can occur on actual control charts.
Processing Control Strips
Once control charts are established, control strips
must be processed on a regular basis. Each color
product has a particular control strip with a particular
format. In a sink-line process, a control strip should
be processed with each run of production film because
of human variables. In continuous (machine)
processors, control strips should be processed as
follows:
Before processing production work at the
beginning of the workday, or shift, or after
a long shutdown, such as a weekend.
Along with production work, at various times
throughout the day.
At the end of each workday, or shift.
After any chemical or mechanical change. Be
sure to indicate this change on the control
chart.
Whenever fresh chemicals are used in the
process. Make a note of this on the control
chart.
2-34
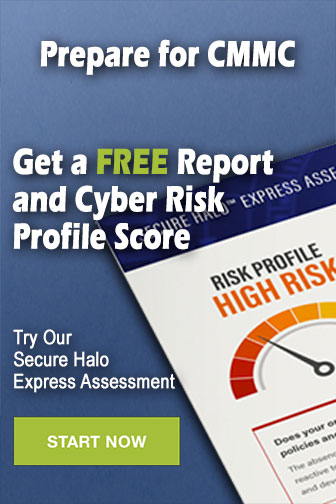