PROCESS EVALUATION
Pre-mission validation must be performed on the
processing system before attempting to process mission
material. These tasks must be performed so the system
is operating within acceptable, established limits for
that particular mission. Six tasks must be performed as
follows:
The processing machine must be checked and
verified to be operating correctly. This includes
solution levels, transport system, temperature,
replenishment rates, and water supply.
The measuring equipment, such as
densitometers and pH meters, must be calibrated
properly to ensure valid, reliable data.
The processing, printing, and support
equipment must be checked and verified to be operating
properly.
The composition of chemical solutions must be
verified to be correct before processing mission
material.
The sensitometric properties of photographic
materials must be certified to be within established
standards.
A scratch test must be conducted to ensure all
the rollers are operating properly and none of the guides
are out of adjustment.
Once the pre-mission validation is complete, you
are prepared to process the actual mission material.
Before processing the film, you must attach a leader tab
to the roll of film. The leading end of the film must be
cut straight before splicing it to a leader tab. A piece of
7-mil Estar base film may be used as a leader tab.
Processed X-ray film works well also. The leader tab
should be about 12 inches long and cut to the same width
as the film being processed (except when used to lead a
control strip).
Mission processing includes the following
procedures:
Protect the material being processed from dirt,
dust, condensation, and other solutions, such as oil and
water.
Avoid applying excessive force to the surface of
the film; abnormal stress can cause pressure
sensitization.
Inspect the material being processed for
physical defects before machine processing. Defects,
such as tears, crimped film edges, and defective splices,
can cause the film to jam in the processor.
Ensure the film is processed in a processor that
has been certified beforehand.
Monitor the processing temperatures and the
transport and replenishment rates while the film is
being processed.
Monitor the film exiting the dryer for correct
dryness, possible defects, and image quality.
Follow the instructions concerning the storage
of film (before and after exposure) carefully.
POST-MISSION IMAGE EVALUATION
After processing, the mission film is subjected to
stringent post-mission evaluation for the following
reasons:
To determine whether or not the process met
desired sensitometric goals and to provide feedback for
process adjustment
To reveal improper procedures or techniques
and to identify defective materials
To identify malfunctioning equipment
The post-mission evaluation should include three
phases: image quality, image analysis, and laboratory
evaluation.
Image Quality
The mission film must be inspected for defects,
such as fogging, streaking, pinholes, and shadows.
These defects are caused by foreign matter in the camera
or on the aircraft window from which the photographs
were taken.
You should also look for superficial defects, such
as film tears, dirt, scratches, abrasions, or foreign marks.
Defects found should be described and reported as to
4-37
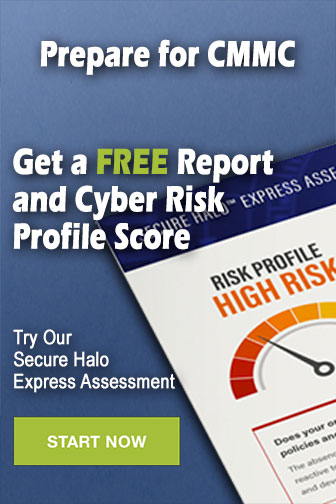